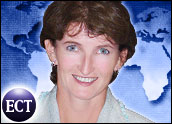
So your small business is experiencing better-than-expected growth,and you’re ready to take the next step and expand globally? Think aboutwhen you go shopping — more often than not, you may notice phrases like”Made in Mexico,” “Made in Sri Lanka” or “Made in Italy.” Perhaps they’reon your clothing tags, your daughter’s new doll, the towels in yourbathroom or the radio on your desk.
This is all part of living in a global economy. Besides fulfillingcountry of origin marking requirements, what are the factors behindthose tags? How did the stylish wool sweater come to be sourced acrossthe water in Italy? Or who decided Egypt would be the best place tosource cotton towels?
While there are multiple factors going into suchdecisions, following are 10 basic points companies should keep in mindwhen looking to source from around the world.
1. Total Landed Cost
It is easy to focus on the lowest unit cost andassume that’s the best way to go. However, unit cost is just one ofthe pieces completing the total cost equation. Other factors includetransportation, customs and duties, brokerage services (both at originand destination), banking fees, financing, and insurance, to name afew.
Further, there could be additional, unexpected costs. If customsdecides to examine the freight, you should add in charges for theexamination and local coordination charges.
What if fumigation isrequired? More charges.
Any delays in the supply chain could resultin expedited freight charges in order to meet the target deliverydate. While these may not occur, it is best to plan for the worst, andhope for the best.
2. Product Quality
The quality of the product has ramifications overand above the unit cost on the balance sheet. Quality needs to bedefined so that both the supplier and buyer understand and are inagreement. If there are issues with the quality of the product, it ismuch harder to address them with a vendor through cultures, time zones, andgeographies, than if you are meeting with a local supplier.
Poorquality affects everything downstream — most obviously the rate ofreturns by dissatisfied customers. Returns drain the business, takingup resources that are more typically focused on getting good productout to the market, not receiving bad product back in. Defective productmay need to be sold at a discount or written off as a loss — bothaffecting the bottom line.
A key part of an efficient supply chain ishaving quality product all the way through it. In some cases, it may bea case of trial and error. However, over the years, as relationships grow,some suppliers stand out as offering a consistently superior product.Those are the relationships to nurture.
3. Logistics Capability
All the great products and quality will meannothing if you are unable to get the goods to market. What type oftransportation is available, both domestically and internationally?After all, you’ve got to get the goods to an airport or seaport fortransport; is there a reliable transportation infrastructure in thecountry? Are you relying on a well-fed yak to negotiate a trickymountain pass to get to a major port, or is there a sound transportationinfrastructure from the sourcing/manufacturing origin point to theport?
Once the freight is ready for international transport, is therespace or lift available? Seasonal fluctuations and weather should betaken into consideration. The impact of last year’s hurricane season on theGulf Coast of the U.S. is a great example. Katrina affected thelogistics of industry and business far beyond the immediate region.
It is important to have the flexibility with service providers to quicklyimplement alternate plans in case the primary plan or transportationlane becomes unavailable.
4. Location, Location …
At the risk of sounding like a real-estate agent,consider location, location, location. The close proximity of acountry may make it a more attractive source — Canada is a case in point.Canada is the largest trading partner of the U.S., both for imports and exports; in fact, it is the largest recipient of U.S. goods.
In thesame vein, Mexico is the second largest importer of U.S. goods, and thirdas a source of imports to the U.S. behind only Canada and China. Theclose proximity leads to benefits like doing business in the same, orclose, time zones.
In addition, common cultural differences andsimilarities, including language, are known, as many of the populationsin the three North American countries have their origins or families inthe neighboring countries.
NAFTA has also done a lot to easerestrictions on trade between the countries.
5. Trade Regulations
There are many governmentalregulations that can enhance or detract from the ease of doing businesswith a given origin. For years, there were quota restrictions with respect totextile imports from China. That restriction was removed inJanuary 2005, leaving China trending toward sourcing up to 50 percent of theworld market share of textiles.
Before any sourcing decision is made,it is imperative that all trade incentives or restrictions are carefullyevaluated. It is also essential to be familiar with documentationrequirements for U.S. customs clearance. There are many governmentsponsored publications, brokers or consulting organizations availableto help educate an importer in the legal requirements of internationaltrade.
6. Financial Considerations
Any discussion of buying and selling would be incompletewithout evaluating the financial aspect, in addition to looking at theactual cost of goods. What terms can be negotiated? What is the riskwith a given manufacturer? Is more insurance required to source from asupplier in Vietnam versus Hong Kong?
Can your excellent credit termswith your domestic bank be leveraged to benefit the suppliers’financial picture, resulting in less risk and cost to the buyer? Howwill the increased transport time — resulting in tied up inventory –affect your cash-to-cash cycle?
7. Time to Market/Responsiveness of Supplier
Time to market isbecoming an increasingly critical factor in sourcing decisions. Ifone’s competitor has product available more quickly, the result couldbe lost market share and, more importantly, lost revenue. It isimportant that your supplier be receptive to, and able to accommodate,change.
Perhaps the product needs to be tweaked slightly, or sales areexceeding expectations and production needs to be ramped up. Is thesupplier in a position to do this? If the industry is subject to whims — think fashions for teenage girls, for example — sourcing in Latin America may make sense with its proximity to the end market and quicker transport time.
8. Value-Added Services
Are there additional services available atorigin to add value to the product? Is it less expensive and moreefficient to have garment hang-tags attached at the factory orconsolidation site prior to shipping? This can expedite the deliveryin the U.S. by bypassing a facility to do the same work, most likely at ahigher labor cost than if done at origin.
Does the supplierguarantee it will pack the freight to ensure it arrives intact atdestination? A new importer might make the mistake of cutting cornerson the packaging and dunnage when importing honey from China. Theresult could be steel drums bouncing around an ocean freight containerfor 12 days on a vessel, then five more days on the rail, only to havehoney oozing out of the container from leaky drums when it is opened atits Chicago destination.
Such a situation — sadly, not fictitious — hasthe consequence of lost product, lost sales and significant cleanup –all more costly than investing in the original dunnage at origin.
9. Communication/IT capabilities
How will you know what has shipped? Is your supplier a real-time,Iinternet-savvy, information-sharing partner? Or will you be waiting for documents typed on an IBMSelectric to be pouched over in a DHL envelope? An open line ofcommunication between the supplier and buyer is imperative. Late,missing or inaccurate documents can cause delays of customs clearanceand, ultimately, delivery to destination.
Inaccurate productinformation may result in swim shorts going to Seattle in September andumbrellas to Phoenix, requiring additional freight and time to correctsuch errors. E-mail and the Internet, and good old phone calls, can goa long way toward supply chain efficiency.
10. Human Toll
The human toll is often overlooked, but it can be acritical part of the sourcing decision; there is a real human effort required to visitand work with suppliers overseas. On top of airfare, hotels and food — allsubstantial expenses in their own right — is thecost of time away from the office and family.
If someone is spending aday or more traveling, that is time away from the office and, presumably,the work that would be done there. Fatigue comes into play as thetraveler works to get over jet lag and prepare for meetings. Inaddition, cultural differences need to be thought of ahead of time inorder to avoid inadvertently insulting the hosts.
Don’t arrive inCairo and expect to work on Friday; don’t be surprised in India if, asa female, you are told you may not use the exercise facility in thehotel during “gent’s time.” Be prepared to be open to different foods,dress — even toilet facilities. There are numerous publicationsavailable to coach a traveler on acceptable customs in the destinationcountry. Being even slightly familiar with them and making the effortwill be appreciated by your hosts.
The above represent a handful of key factors to consider when makingglobal sourcing decisions. Whether you are new to importing, or justconsidering sourcing from new a new region, remember that there arenumerous resources available to help make a well thought out choice.Once an informed decision is made, there is a huge opportunity to enjoyconducting profitable business in the global market.
Sara Ireton is a supply chain management consultant forJPMorgan Chase Vastera. She has been involved in the international trade environmentfor over 15 years, working with vendors, suppliers, serviceproviders and clients globally, covering issues from origin operationsand customer service to supply chain visibility and quality.