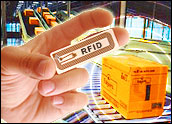
The use of RFID technology in the retail industry has been increasing, albeit tentatively, and the debate over RFID in general continues unabated. Meanwhile, proponents are finding that RFID adoption is easier in the manufacturing sector and upstream in the supply chain, in areas such as asset tracking and inventory management, as well as security-related, government-driven applications, such as international air travel.
Increasingly, RF or radio frequency technology is being applied to a variety of areas — including environmental monitoring and management, insurance, the pharmaceutical industry, and transportation systems management — as part of wireless sensor networks, or WSNs.
Low power mesh networking, sensing and real-time location is a combination whose time has come. “Today’s enterprises crave visibility across the entire supply chain and real-time data about objects — and people — moving through the system, as well as the condition of those objects. All this can help businesses streamline operations and provide better customer service,” said Brian Bohlig, vice president of marketing at wireless sensor network systems and software vendor Arch Rock.
Tracking Errors
A leader in the design of RFID and contactless smart card, smart label and smart tag chips with an approximately 35 percent market share, Philips Semiconductors, with the help of IBM Business Consulting Services, puts its products to good use within its organization.
Phillips, as with any successful business large or small, continually seeks ways to improve profitability by getting a better handle on its fast-changing and fast-moving product inventory.
This is no simple task, especially when the organization includes 20 large manufacturing and distribution facilities with approximately 36,000 employees and hundreds of sales organizations spread across 60 countries.
Until recently, workers at Philips’ manufacturing and distribution centers manually scanned bar codes to capture inventory information, which required using a bar code reader with a direct line of sight to each carton.
Information was then entered manually into the company’s enterprise resource planning (ERP) system, according to a case study published by IBM Business Consulting Services.
This tracking process proved to be error-prone as well as time-consuming, often resulting in discrepancies between actual product status and the status recorded in the ERP system. This, in turn, caused problems for both customers and customer service staff, who shared and acted upon erroneous information.
Sense and Respond
“We recognized that we had to re-engineer critical processes such as capturing inventory data at our production and logistics facilities, and updating our ERP systems,” explained Philips Semiconductors’ Global Strategic Alliances and Programs Manager Heinze Elzinga in the case study.
“Accordingly, we saw the tremendous opportunity to leverage our own leading edge RFID technology to deliver real-time insight into our business critical supply chain processes and inventory information,” he added.
Philips and IBM Business Consulting worked together to design, develop and implement a next-generation manufacturing and distribution supply chain that enables increased efficiency and improved customer service through a methodology that IBM calls “sense-and-respond information management.”
Combining Intel RFID with its own ICODE technology, IBM WebSphere and DB2 software components, Philips re-engineered 13 supply chain processes and designed a systems architecture that integrates sensors, RF chips, applications, databases and user interfaces to connect networked RFID readers with Philips’ warehouse management and order management systems, in real-time.
Improving the Process
Philips is now planning to roll out the supply chain system to all of its manufacturing facilities and distribution sites — beginning by tagging cases of one of its high-demand integrated circuit products manufactured at its Kaosiung plant in Taiwan and distributed via a distribution center in Hong Kong.
Using embedded miniature antennae, the RFID tags send bits of essential stored information as signals to a receiver that reads and forwards the information to a server.
The server automatically updates the company’s ERP system, thereby enabling Philips to establish a real-time connection between its manufacturing and distribution centers and its ERP application.
In addition to real-time updates, the RFID tags enable Philips to use more specific criteria to track products than under its previous, bar code-driven approach. “With data embedded in the tag, we have a unique identifier, allowing us to manage our inventory more efficiently than ever before,” Elzinga said.
“Plus, unlike barcodes, RFID tags can be read at any angle and from a distance, so we have more flexibility with how we manage physical space at our facilities,” he noted.
As a result of re-engineering its supply chain processes, Philips has increased inventory turns, improved stacked lead time, optimized space utilization, enhanced delivery reliability and warehouse efficiency, and improved customer service, according to the case study.
More specifically, the receiving step of the process has dropped from 40 seconds to 20 seconds, sorting and batch tracking processes have been reduced from 20 seconds to 8 seconds, and the palletization process has dropped from 20 seconds to 10 seconds.
On the back-office side, Philips now generates customer invoices much more quickly, resulting in shorter billing cycles by reducing the information latency in its ERP system.
Sensors and Actuators
Whereas RFID applications are making headway in the manufacturing sector, the going’s been tougher in the retail industry.
“The only people really doing RFID are Wal-Mart, the Department of Defense, Marks and Spencer in the UK and a few others. There’s been very little implementation,” Richard Mader, executive director of the National Retail Federation’s ARTS (Association for Retail Technology Standards) told CRM Buyer.
There are a variety of reasons for that, technological constraints and privacy concerns prominent among them. However, there is another area in which information systems and application developers see promise for RF technology: sensors and actuators.
“Offering much more info than simple RFID, sensors can monitor and record conditions like temperature, humidity, pressure, wind direction and speed, illumination intensity, vibration intensity, sound intensity, power-line voltage, chemical concentrations, pollutant levels and vital body functions,” explained Kelly Sims, speaking for the IBM Software Group.
“Actuators can send and receive real-time data from the sensors — sometimes thousands of them — to learn about remote conditions and locations. And when sensors and actuators are mixed with RFID, well, then some pretty gee-whiz applications are created.”
Myriad Applications
RF chips have already been used in a wide variety of applications in many different types of organizations.
In the pharmaceutical industry, IBM is using RFID and sensor technology to help manufacturers and distributors protect consumers from counterfeit drugs. It is also working with one of the largest insurers in the UK, enabling their clients to receive customized insurance pricing by allowing safe drivers to put a sensor on their car, Sims explained.
“The cars are tracked, and are given discounted prices based on how aggressively they drive, at what speed, etc.,” he added.
In Sweden, the City of Stockholm has worked with IBM to design and launch a pilot traffic congestion pricing system designed to reduce traffic and pollution, and increase the use of public transportation.
“The project has yielded a 25 percent traffic reduction in the first month of operation, removing 100,000 vehicles from the roads during peak business hours, while resulting in a corresponding increase of 40,000 mass transit users per day,” Sims said.
Inherent Benefits
Wireless sensor networks offer a number of advantages over traditional RFID implementations, explained Arch Rock’s Bohlig.
“First of all, the ability to rapidly deploy a multi-hop network (RFID is single hop only) allows WSNs to be used in a number of ad hoc/temporary situations — such as emergency response, defense, business and safety applications — where tuning the deployment environment is either impossible or impractical,” he continued.
“Furthermore, the ability to locally store data when the tag/node is ‘out of network’ and then download that data when the tag or node comes back into a network provides an audit trail with time line, environmental conditions and location.
“Another advantage is the ability to push logic to the nodes themselves without the need of nearby infrastructure. This allows for new applications, such as real-time warning of proximity to hazardous substances or enforcement of safety rules in the operation of heavy machinery,” Bohlig concluded.